PLASTICS COULD HELP BUILD A SUSTAINABLE FUTURE – HERE’S HOW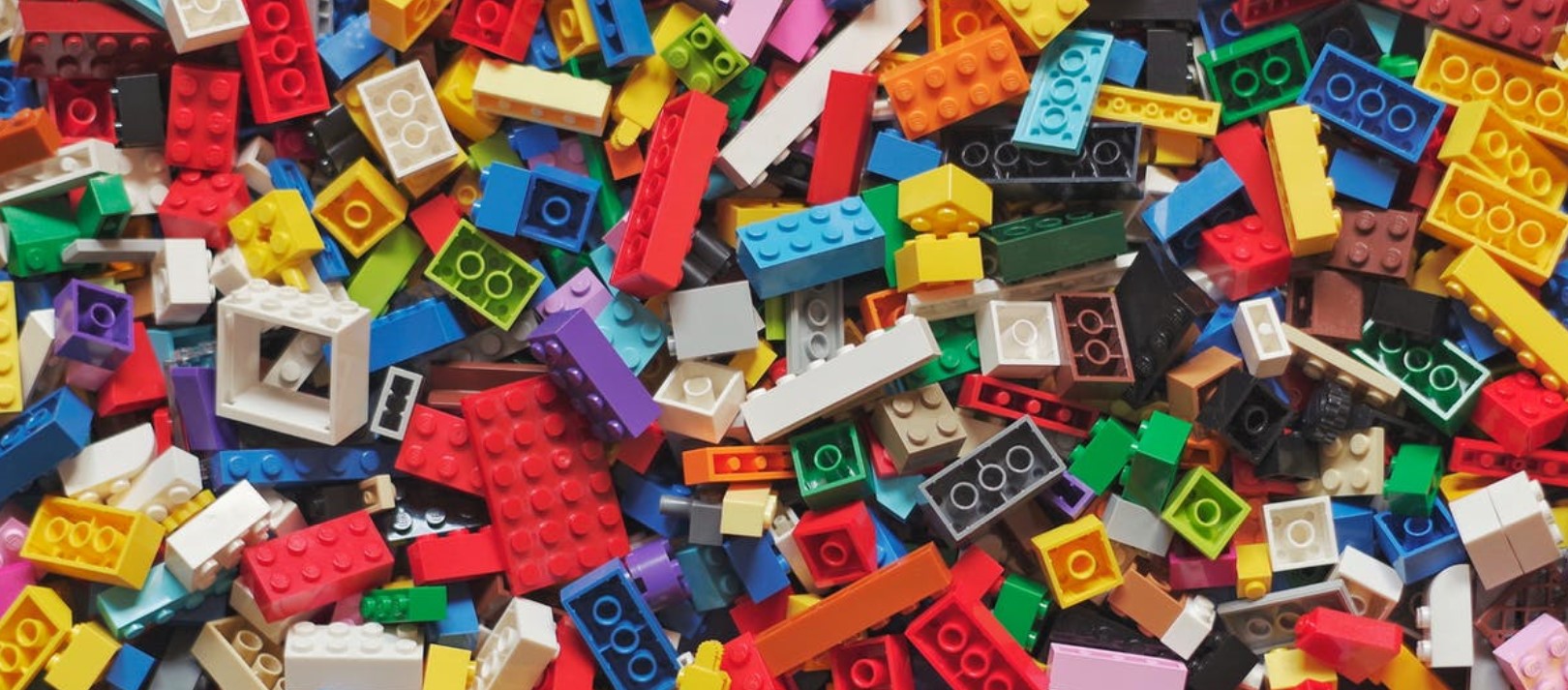
This article by Sibele Cestari first appeared in The Conversation on 12 August 2020.
20 August 2020
The disposal of plastics is a global problem. They are nearly indestructible in natural conditions but are discarded worldwide on a large scale. The world produces around 359 million metric tons of plastics each year. Nature cannot address the amount of their disposal at a speed fast enough to prevent harm to living beings.
There is a consensus that plastics are an unsustainable material. And yes, plastics are certainly an enormous problem, but they don’t necessarily have to be. The main issue is with our linear economic model: goods are produced, consumed, then disposed of. This model assumes endless economic growth and doesn’t consider the planet’s exhaustible resources.
Most people believe that plastics recycling is severely restricted: that only a few types can be recycled at all. This is unsurprising. The proportion of plastics that are recycled is minimal. The UK, for example, uses five million tonnes of plastic each year, and only 370,000 tonnes are recycled each year: that’s just 7%.
But all polymers are, technologically, 100% recyclable. Some of them have the perfect cradle-to-cradle lifecycle: they can be used again and again to produce the same goods. Some plastics can be reused just as they are by shredding an object into flakes, melting it, and reusing.
Such recycled plastics may have lower mechanical properties compared to virgin plastics, because each time you melt and process a plastic, the polymeric chains degrade. But these properties can be recovered by mixing it to additives or virgin plastic. Examples of successful industrial recycling include PET – poly (ethylene terephthalate) which is used to make soft drinks bottles, and polystyrene.
All of the rest can technically be reprocessed into new materials for different applications. In the final instance, any plastic waste can be shredded and used as filler for asphalt, or be pyrolysed to produce fuel. The Japanese company Blest Corporation already sells a portable machine to convert domestic plastic waste into fuel in a simple, affordable way.
The problem is that recycling much of this plastic waste is currently unfeasible and unprofitable. Polymers such as rubbers, elastomers, thermosets and mixed plastic waste are comfortably labelled as ‘unrecyclable’ by the recycling sector. But the amount of these materials all over the world is frighteningly large and keeps on growing. What if this plastic waste could be used to produce something useful to society?
Many universities and entrepreneurs are attempting to do this. Most solutions target mixed plastic waste and suggest applications different from the original ones. For example, several groups have developed building materials made of plastic waste.
Plastics are strong, durable, waterproof, lightweight, easy to mould, and recyclable – all key properties for construction materials. So what if all of this plastic waste could be converted into building materials for low-income populations? Existing initiatives are promising, but not yet reproducible on an industrial scale.
Plastic building blocks
I study plastic waste with the specific aim of finding interesting ways to remove it from the environment. Since 2009, I have developed a number of building materials made of post-consumer plastics mixed with different waste-stream materials. From agricultural wastes such as sugarcane bagasse – a by-product of the sugar industry in Brazil – and coffee dregs, to concrete waste and construction debris, compounded with recycled plastics, there are many ways to obtain materials to produce bricks, roof tiles, plastic lumber and other useful elements for building.
Our team is currently trying to develop a viable building block made of recycled plastics. We have prepared a range of prospective materials using a mix of virgin and recycled plastics – coloured PET bottles, polypropylene, polyethylene – and other local waste-stream materials – hemp, sawdust, concrete waste and red mud.
We are currently adjusting the properties of the materials for the rotomoulding process, a plastics moulding technology which is ideal for making large hollow articles. We want to use the maximum amount of recycled plastics in this block. Blocks made of 25% recycled plastics have performed extremely well in mechanical tests. Next we’ll try 50%, 75% and 100%.
We are also thinking about the aesthetics of the blocks. Blends of recycled mixed-colour plastics usually end up with a grey or black colour. To enable colour, we are preparing blends of virgin or recycled plastics to overlay the main bulk of the block.
Building from waste
So perhaps plastics are not necessarily the problem. They can be part of a pathway towards a more sustainable way of living. Using a natural or renewable resource is not necessarily environmentally friendly. The ecological footprint of a polymeric material is smaller than that of natural materials, which have a sizeable demand on arable land, clean water, fertilisers and regeneration time.
According to the Global Footprint Network, before the pandemic we were demanding 1.75 times the available resources of the planet. Working with the “unrecyclable” waste and developing plastics alternatives to natural materials may reduce this demand and leave a cleaner and more sustainable planet for the next generations.
Building materials made from recycled plastics are not yet widely used in the construction industry – prototypes have mainly been used for demonstrative installations. It will take political will and widespread environmental awareness to encourage more investment into the potential in plastics recycling.
But hopefully the tide is beginning to turn, as a consequence of the increasing pressure from public opinion about the plastic pollution matter. Thanks to the engagement of government and industry to the idea of a circular economy, it seems that there will be an opening in the market – and in people’s minds – to welcome plastic initiatives to replace conventional building materials.
Sibele Cestari is a Research Fellow in Polymeric Materials at Queen's University Belfast. ‘The Conversation’ is an independent source of news and views, sourced from the academic and research community and delivered direct to the public. This article is republished under a Creative Commons license.
Media enquiries should be addressed to the Communications Officer at Queen’s University Belfast.
Back to Main News
Top of Page